The breadth of MechE
Changes to the technological landscape, and to the needs of industry and society, are rapidly expanding the field of mechanical engineering into new areas, driving increased interdisciplinary collaboration, and even yielding new specializations.
“We are continuously pushing the boundaries of our own fields, and redefining what mechanical engineering is,” says Faez Ahmed, d'Arbeloff career development assistant professor of Mechanical Engineering.
Across MechE, faculty and staff are engaging in cutting-edge research at the frontiers of a new vision for mechanical engineering, with teaching and exploration at the intersection of engineering and physics, math, electronics, biology, computer science, and many other fields of study. From the nanoscale to the macroscale, across communities, climates, regions, and geographies, and from the ocean floor to the far reaches of space, the incredible breadth of work underway in MechE is transforming ideas and insight into progress.
“The classical mechanical engineering department that you’re thinking of might have cars, might have steam engines – we have all of those things, but we go so far beyond that,” says Anette (Peko) Hosoi, Pappalardo Professor of Mechanical Engineering.
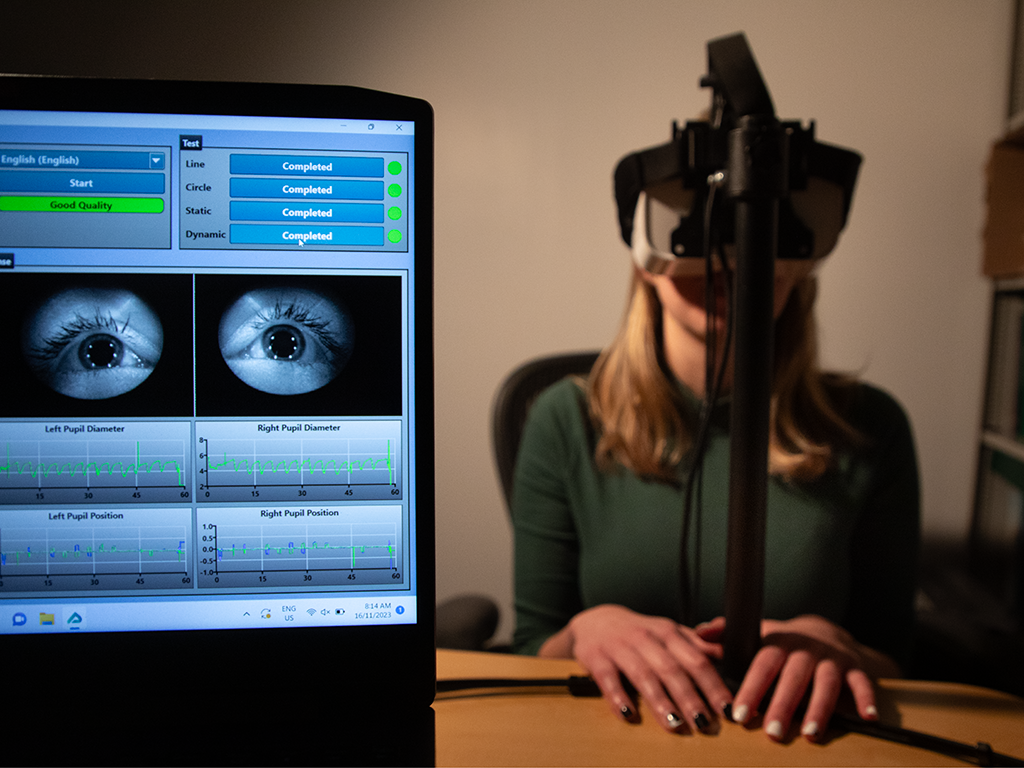
Sensory processing in sports
Close your eyes, extend your arms, and bring one finger to touch the tip of your nose. The ability to complete this or similar tasks, aided or unaided by sight, is owed to a sensory concept called proprioception. Proprioception involves a variety of complex sensations that allow you to sense the position and movement of your joints, along with the length of stretch in your muscles. These sensations create awareness of your body's positioning.
“Proprioception, basically, is ‘how well do you know where your limbs are,’” explains Hosoi, co-founder of the MIT Sports Lab. “If you have poor proprioception, you’re more prone to injury and, when you’re tired, stressed or sick, proprioception is one of the first thing your brain lets go of.”
Hosoi’s core research interests bring together fluid dynamics, bio-inspired design, and sports data and technology to tackle problems at the intersection of biomechanics, applied mathematics, and sports. Mixing experimental work, numerical simulation, and theoretical analysis, and combining elements of engineering design and mathematical optimization, her work has been used to guide the engineering design of robotic swimmers, crawlers, burrowers and other mechanisms.
Understanding proprioception has applications in robotics, AI, and other mechanical designs, and of course, for keeping athletes healthy and at the top of their game. In a study aimed at understanding whether there are times during the semester when their proprioceptive ability might be lowered, Hosoi and her team are working with MIT varsity athletes to measure proprioceptive abilities.
The measurements are made in collaboration with PrismNeuro, a company focused on advanced human performance and founded by MIT alums. One part of the experiment is eye tracking, the other involves having the athlete place their feet on a tilt plate with a stopper that moves the plate to random positions. The athlete is then asked whether the plate tipped a little or a lot, and the team measures how well they perceive the angle of their foot.
“We measure throughout the semester to understand times when proprioceptive ability is low, which are times when the athletes would be more prone to injury,” Hosoi says. “That’s information we can give back to the coaches and say ‘hey looks like everyone is really stressed out with midterms right now, maybe go easy on them’ – the coaches have been really receptive.”
Research in the MIT Sports Lab seeks to improve athletic performance and equipment, advance understanding, and create actionable insights. Other projects underway involve a study to better understand possible differences between men’s and women’s soccer, a data-informed look at judging in aesthetic sports, like gymnastics, martial arts, or BMX, and studies of the physical performance of professional athletes to determine how good they are at making decisions on the court.
“It’s hypothesized, but not known, that women’s soccer is different [from men’s soccer],” says Hosoi. What is known, she says, is that women suffer from more anterior cruciate ligament (ACL) tears than men, presumably from different stresses. “We can we take tools that have been developed for fluid dynamics and turbulence to quantify the differences, then see if that translates to different stresses on the body.”
Using an accelerometer and gyroscope built into the sole of the cleats of MIT men’s and women’s soccer, MIT Sports Lab researchers are trying to better understand what is guiding players’ motion on the field. “Women’s sports equipment is typically designed via ‘shrink it and pink it,’” says Hosoi. “Understanding of the mechanics and the flow of the game instead, can translate into better equipment design – and, perhaps, fewer injuries.”
DeCoDE-ing product design
Faez Ahmed, assistant professor of mechanical engineering and ABS career development assistant professor of mechanical engineering, envisions a world where anyone with a great product idea can access the tools needed to bring their concept to life.
“There are many people with great ideas, but if a person sitting in a remote part of the world wants to create a new product, right now they have to learn CAD software or simulation software, then maybe they have a chance,” he says. “We’re looking at how we can democratize design with the help of AI models.”
Ahmed leads the Design Computation and Digital Engineering (DeCoDE) lab, where research is focused on developing new machine learning and optimization methods for complex engineering design problems and on making generative AI models more precise and accurate. DeCoDE research aims to assist human designers in creating better products and improving the design of complex mechanical systems – including innovative designs for faster cars and better aircrafts, bicycles, ships, and more – and to create a world where humans and AI can design together to solve global challenges.
Humans understand and present the initial parameters, then “AI can look at thousands of related designs and options and quickly present drawings and options that humans may not have thought about to come up with designs that are either better or more innovative.”
The DeCoDE team approaches design challenges by fundamentally understanding them as mathematical problems, formulating them into generalized machine learning and optimization problems, to develop methods that are applicable to a wide variety of engineering problems at different scales. One of Ahmed’s favorite challenges the team has tackled is the linkage mechanism problem.
Machines depend on mechanical linkages, an assembly of connected systems to manage forces and movement, but creating these assemblies grows more complex as more components are added. “In mechanical engineering, one of the fundamental things we study is how machines are designed – four bar or six bar mechanisms are a fundamental concept – but when the number of linkages starts increasing, it becomes an impossible problem for humans to solve."
Demonstratively, tracing just the letter M as a linkage mechanism equation entails hundreds of pages of complex explanation. Most current databases include tens of thousands of mechanisms. Ahmed’s team created datasets with 100M mechanisms, and then trained their model with the data. With the design output, they’ve successfully manufactured products – in one case, a single-motor design that’s capable of writing out “M-I-T.”
“What we’re really solving is a mapping from design space to functional performance space and, given some functional requirements, we can go back to the design space and find the design. This is exciting because it applies to so many other domains – from molecule design to transportation systems – and no other method can solve it.”
DeCoDE’s datasets are publicly available on the lab’s website, a concerted effort to help jumpstart research for the community. “One of the biggest gaps in engineering is a lack of datasets. People focus too much on data-driven method development, but really the methods can’t do much without having data out there,” says Ahmed, pointing to similar trends in computer science in the early 2000s.
“While there was substantial progress initially, the field saw monumental advancements following the creation of Stanford’s ImageNet dataset. There was a cultural change. Today, our focus extends beyond individual contributions from a group; it's about the synergistic progress of the entire domain and requires community effort.”
Open-source underwater autonomy
Early investments in marine vehicle technology focused on ‘dull, dirty and dangerous’ tasks, with control software that guided fairly straightforward point-to-point movement. Today, autonomous Underwater Vehicles (AUVs) are used for a wide range of civilian, commercial, and military applications – including seafloor mapping, construction, security and defense, climate monitoring, oceanography, and marine research. Traveling unmanned through the ocean for long durations, AUVs need to be able to communicate, avoid collisions, and manage a host of other navigation and environmental challenges without human intervention or access to GPS.
“There’s a difference between autonomy and control – control is deciding how to get from point A to point B, where autonomy is deciding what point B should be,” says Michael Benjamin, principal research scientist in MechE’s Center for Ocean Engineering. “As vehicles have become more capable in sensing and communicating, deciding where to go is no longer just a scripted set of points – it’s being left up to the robots.”
Custom tasks and modern applications require custom software, which is expensive and resource intensive to create. Benjamin, who leads the Marine Autonomy Lab, designs algorithms and software for autonomous marine vehicles, with a focus on making marine autonomy an accessible commodity.
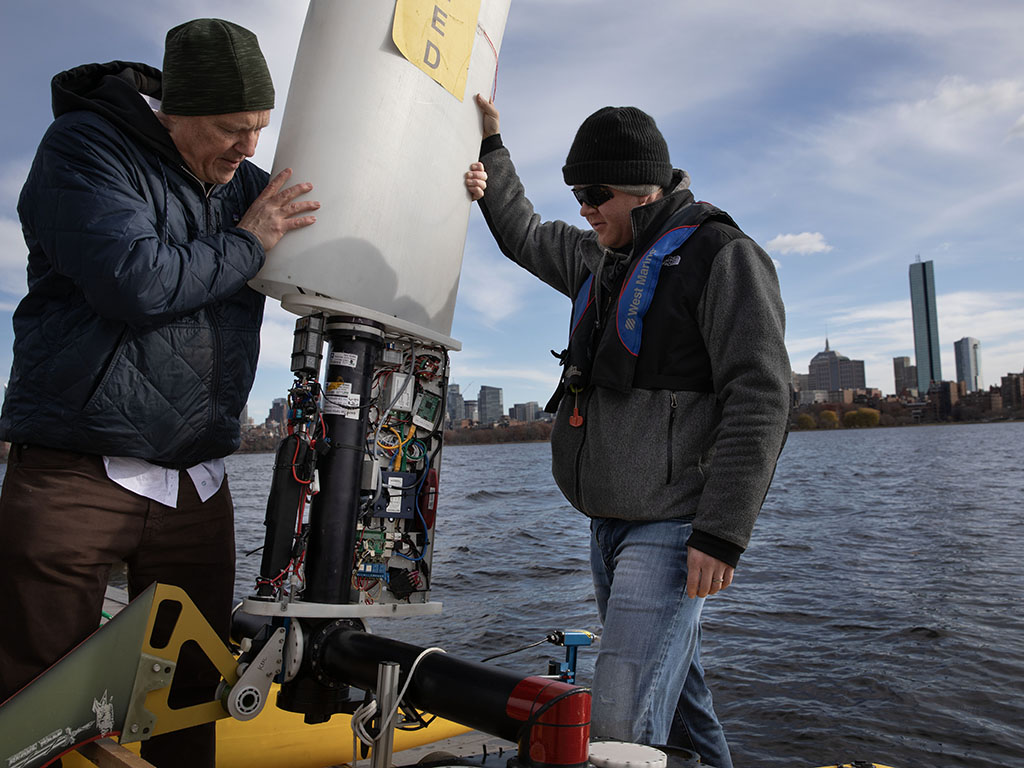
“If autonomy is a commodity, scientists who are using the software can focus on their area of expertise – which may be ocean sensing, or acoustics, or any number of areas – the autonomy of the robot, then, is just a means to do something,” he says. “If the vehicle and autonomy are technologies you can use, the group of people who can explore the ocean with robots becomes a much bigger group.”
Benjamin came to MIT as a post-doc in 2002, while also working as a civilian in a U.S. Navy research lab. He joined MIT as a research scientist in 2011. In both environments, he says, it was common for code to be discarded at the conclusion of a project. Students could spend years developing new code instead of building on what was previously created, which Benjamin found frustrating. Working with his then lab-mate, Dr. Paul Newman, who is now a professor at Oxford University, he set out to create an open-source codebase that can outlive any one vehicle, or any one researcher.
Mission Oriented Operating Suite - Interval Programming (MOOS-IvP) is a set of open-source C++ modules for providing autonomy on robotic platforms, in particular autonomous marine vehicles. Some 40 work-years of coding have now gone into developing the codebase, which is used at MIT and beyond. Instead of writing code and creating software from scratch, researchers can innovate using what’s already available, making it possible to begin other research aspects sooner.
In Benjamin’s group – where there’s “a large emphasis on field experimentation, fixing, and improvising”– recent projects include autonomous vehicles for aquaculture applications and software for companies working on hybrid, land-to-sea robots. As students work on projects and create particular autonomy capabilities, they contribute to the codebase. As a byproduct, he says, the team is improving the infrastructure behind the scenes and making it more powerful so each new project can start from a better position.
“If everyone who wanted to explore the ocean had to start by writing a simulator and a control algorithm, it would be very difficult to accomplish anything,” he says. “We’ve increased the number of seats at the table – which means the various minds you’re bringing to the work increases, too.”
Cells as building blocks
Ritu Raman, assistant professor of mechanical engineering and d’Arbeloff Career Development Professor of Engineering Design, conducts research in biofabrication, a field where living cells are used as a building material, in the way other engineers might build with synthetic materials.
“As a mechanical engineer, I’ve long pushed back against the idea that people in my field only build with metals, polymers, or ceramics,” she says. “I’m interested in building with biology.”
Current research in Raman’s lab is focused on building motor control systems (skeletal muscle and the nerves that control its movement) from scratch by patterning cells and proteins in precise 3D architectures. She aims to use these tissues to restore mobility in patients with motor disorders caused by traumatic injury or illness. Her team is also interested in using engineered muscle as an actuator to power soft and adaptable “living” robots.
“Engineering functional muscle tissue is important for a range of applications in medicine and robotics,” she says. “Using living materials helps us make implants or machines that can dynamically sense and respond to their surroundings in a way that more traditional building materials (like metals and polymers) cannot.”
Raman’s team recently introduced Magnetic Matrix Actuation (MagMA), a vibrating gelatinous mat that can used for growing muscle tissue. The vibrating mat is composed of magnetic microparticles embedded within a soft hydrated gel that allows the researchers to impose forces on cells while they are growing and maturing. They found that muscle grown on MagMA gels could be programmed to grow highly aligned muscle fibers, generating strong and coordinated contractions.
“There’s evidence from biology to suggest that a lot of types of cells are responsive to mechanical stimulation,” Raman says. “Mechanical forces play a really important role in our bodies and lived environment. And now we have a tool to study that, not only in muscle but in other cell types as well.”
Raman says the gel can serve as a quick and noninvasive way to shape muscle fibers and study how they respond to exercise. Her lab plans to grow other cell types on the gel in order to study how mechanical forces, particularly those generated by exercise, control a wide range of biological processes within our body.
In a separate related study, the team found that exercising muscle grafts after they had been implanted in a mouse with a traumatic injury could accelerate recovery and completely restore mobility to the animals within 2 weeks.
“We found that exercising muscle grafts after they've implanted does more than just make muscle stronger, it also appears to affect how muscle communicates with other tissue, like blood vessels and nerves,” says Raman. “By actively communicating with the implant and exercising the muscle graft, you can actually improve and accelerate recovery timelines.”
Raman’s long-term goal is to teach the next generation of engineers how to build with biological materials so that they can build “biohybrid” solutions to real-world challenges.
Quantum and precision measurements
If you hear the words ‘quantum’ and ‘large’ in the same sentence, the discussion would usually be about something hypothetical or perhaps not experimentally viable, explains Vivishek Sudhir, assistant professor of mechanical engineering and Class of 1957 Career Development Professor.
Historically, when researchers have been able to put mechanical objects into quantum states, it’s been single atoms – but not Sudhir’s group. His team has pioneered several techniques to realize large mechanical objects in quantum states of motion.
“We’ve demonstrated how to prepare kilogram-scale objects in quantum states, opening the door to experimental study of how gravity might affect quantum objects,” he says. This understanding is useful for enhancing the precision of measurements in mechanical objects, and in answering the foundational question of what the true nature of gravity is.
In the modern world, almost every conceivable enterprise—from computing, to GPS, to clocks, to economic systems—depends on precise atomic measurements.
Sudhir’s Quantum and Precision Measurements Group makes some of the most precise measurements of motion, borrowing and developing techniques for quantum measurements and control. His team’s current interest is in making measurements that would shed light on the nature of gravity. Theorists have been trying to build a quantum theory of gravity for at least 100 years, but how to combine physics and gravity remains a puzzle. Sudhir says there are a lot of good reasons to assume gravity is quantum.
“One might ask ‘why is this in MechE and not in Physics?’ I think the answer is that it could be either place, and that’s the beauty of MIT,” Sudhir says. “You don’t need to be in one place, you can be in two places at the same time – which is also a pun for the kind of quantum mechanics we’re interested in doing.”
Working with students in his lab and in the Laser Interferometer Gravitational-wave Observatory (LIGO) Laboratory at MIT, his team is scaling up quantum metrology techniques to gram-scale oscillators, refining quantum technologies based on mechanically-compliant interferometers, and developing mechanical systems that allow for probes of basic physics of motion.
“My undergraduate education was in electrical engineering, my PhD is in physics, now I’m teaching mechanical engineering. I draw freely from all of these areas,” Sudhir says. “It is key for my students to be able to do something similar. One day they may be working on making an oscillator, another they’re building a laser to make an optical measurement.”
He says there’s no scope for anyone in his group to remain siloed in any one area, adding that the first thing he asks his mechanical engineering students to do is to go take the graduate quantum physics course over in Physics.
“At the end of the day, a student at MIT should not just be a technician. They need to be able to form their own ideas, to be able to zoom into the details but also to zoom out to see the big picture.”
Fundamental robustness
Walking into Professor Alex Slocum’s office, one of the first things you may notice is the collection of objects strewn across his granite surface plate table in the center of the room. Each of the items – from precision machined parts, to catalog components, to Lego pieces, to hand tools, including a pair of toenail clippers – “has a purpose in teaching and research,” he says.
Not only can each object be used to demonstrate some engineering concept or catalyze creation of new ideas – the toenail clippers, for example, can offer a lesson in linkages – the way people choose to interact with the items reveals a lot about the way they think, and that’s important. It’s curiosity he’s looking for in collaborators interested in joining his Precision Engineering Research Group (PERG).
His goal is to inspire students to think differently. “If you think like everyone else, or just like an AI system, the human race may never realize the innovations needed to save the species,” he says.
Slocum, the Walter M. May (1939) and A. Hazel May Chair in Emerging Technologies, designs all sorts of machines for all sorts of applications. A common theme is deterministic design, which means relying on mechanics, not hope, to achieve precision – an example is machines that use kinematic couplings (six points of unique very stiff contact to establish the position and orientation between objects) or elastic averaging interfaces (many compliant points contact between objects where errors are averaged over a large number of contacting elements). His team is working to improve energy machines, making them ever more precise, for longer useful life, and to lower the cost to make, operate, and dispose of or repurpose at the end of their life, “for example, what we did for oil and gas drilling needs to now be done for geothermal energy systems,” he says.
In his 40 years in academia at MIT, Slocum has seen a lot of trends in mechanical engineering come and go. The thing that hasn’t changed and that will always be true, he says, is that mechanical engineering is ultimately about bringing ideas into physical reality, and the need for these physical realities will always be present.
“Whatever course you’re studying in, whatever work you do, ultimately there will be a physical reality that’s directly part of it,” he says. “If you’re a mathematician, you’ll need ‘things’ – a pencil, an iPad – and those ‘things’ are designed, manufactured, delivered, and must have an end-of-life plan.”
These physical needs for things evolve across time and with every new innovation in the many areas across MIT. Current realities mean constructing more efficient machines to make the hardware for data centers, or making power mechanisms more efficient so “all things Internet” can operate. This means there’s an ongoing need for mechanical engineers capable of doing the design, manufacturing, and operation engineering, Slocum says, and these engineers must be highly skilled at hands-on problem-solving often in the field when unforeseen issues arise and rapid fixes are required.
“A Mechanical Engineering renascence includes our students and faculty understanding and embracing the fact that nature does not care and physics cannot be fooled,” says Slocum. “The fundamentals are not only as important as they ever were, they are critical for our students to passionately embrace and master.”
He goes on to opine, “as AI gets better and better, and as we ME professors partner with our AI colleagues to encode our knowledge, the bar for our students to master the core mechanics of ME and the “FUNdaMENTALs of design will only rise.” And he is optimistic, “Perhaps MechE might also be thought of as MechExciting!”
AI, robotics, and solar technology – accelerated
Tonio Buonassisi, professor of mechanical engineering, tells a story about a solar-to-fuel problem that existed in the 2010s, a time when the field was driven mostly by chemists. Devices that convert sunlight into fuels using commercial silicon solar cells were only getting a fraction of the expected efficiency. Chemists blamed the catalyst, but the engineers brought in to collaborate viewed the problem differently. They opted to build equivalent-circuit models and, by reviewing various stages in the process, found that a series resistance term was dragging everything down. By redesigning the system, the team was able to improve the system’s sunlight-to-fuel conversion efficiency from a fraction of a percent to 10 percent.
“I get asked a lot, ‘why are you in mechanical engineering, why not chemical engineering or materials science?’” says Buonassisi, noting that he gets similar questions from students about their own path. “For the type of interdisciplinary research we’re doing, mechanical engineering brings together the necessary expertise under one roof.”
Systems thinking is a way to break down a complex system into its constituents to figure out which things are limiting and how to improve, and it’s intrinsic to mechanical engineering. “Design, manufacturing, and systems thinking, among other aspects – our department has these kernels of wisdom embedded, and they’re infinitely practical,” he says.
Buonassisi leads the Accelerated Materials Lab for Sustainability and ADDEPT, a collaborative research center that merges materials, automation, and computation, specifically in artificial intelligence and solar energy. Today, his lab is working to accelerate new materials development in solar, fusion, and electrochemistry by developing high-throughput experimentation and machine learning tools.
“Our research takes place in the center of a triangle – the corners are automation and robotics, machine learning and computation, and domain expertise with a deep understanding of solar technology, electrochemistry, and fusion. The interdisciplinary nature of our work means, to do it well, you have to be at the middle of this triangle.”
ADDEPT stands for Accelerated Co-Design of Durable, Reproducible, and Efficient Perovskite Tandems. Perovskites—a family of materials with potential for high performance, low production costs in solar cells—are a leading contender to augment silicon-based solar photovoltaics in tandem architectures, but the material has known durability issues. That’s something Buonassisi’s team is working to solve, and quickly.
“Our vision, as a lab and within our collaborations, is to set up autonomous labs to impact solar, electrochemistry and fusion. We’re developing high-throughput experimentation that is designed to operate more reproducibly and orders of magnitude faster than human hands with closed-loop machine learning.”
The closed-loop aspect of the experimentation process is important. In closed-loop learning, continuous feedback mechanisms monitor and adjust operations based on outputs or results. Machine learning is very good at is taking in many variables, quickly, and navigating the high dimensional space. This dramatically speeds up the discovery process.
“In a high-dimensional parameter space, changing just one variable at a time would take forever to find the optimal conditions,” he says. “We have a finite time to develop technologies that can mitigate climate change. When you’re under that clock, you have to move a lot faster.”
A big emphasis of the lab is open science. Creating open software and open hardware is important for reproducibility, Buonassisi says, and it also ensures these tools get into the hands of people who can benefit from them the most.
This article appeared in the Spring 2024 edition of our magazine, MechE Connects. For more stories, and for past issues, please visit meche.mit.edu/magazine.